Medical Device & Diagnostics
A Harmonized Framework for Managing Medical Device Quality and REGULATORY Compliance
The AssurX Medical Device Quality Management System: Aligning Quality Objectives with Compliance Requirements
The medical device market is full of opportunities to create life-saving products that diagnose and treat patients worldwide. To meet those demands, the AssurX medical device quality management system is designed to support manufacturers in marketing safe and effective medical devices while demonstrating compliance.
Device and diagnostics manufacturers use the AssurX EQMS to bridge the gap between aligning quality processes to improve product safety, while maintaining compliance with applicable regulations.
AssurX helps enforce compliance with the following regulations and standards:
TRUSTED BY
AssurX Medical Device Quality Management System Features
Manufacturers in the medical device industry and the diagnostics industry must maintain a laser-focus on continuous quality improvement. A modern quality system using paper-based processes and siloed data is no longer viable.
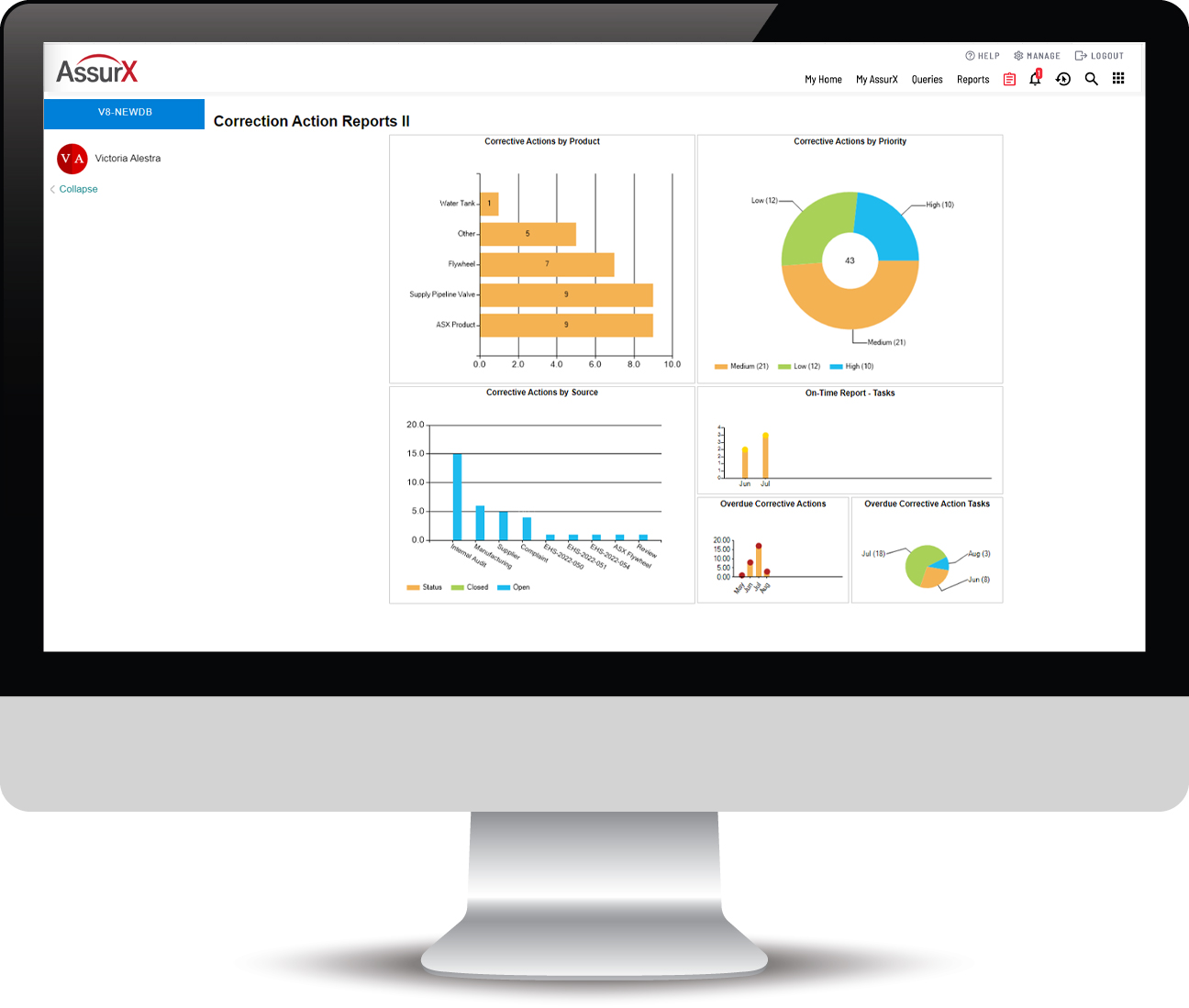
AssurX is built with robust features based on over 20 years of best practices, including:
Overcome Today’s Biggest Challenges for the Medical Device Industry
AssurX medical device quality management system accelerates your quality oversight to correct issues faster and implement preventive measures to prevent recurrence. Maintain a risk-based, proactive posture for efficient problem resolution.
Increased Efficiency
AssurX increases efficiency by integrating processes to close the loop on quality issue faster and confidently. Launch CAPAs at any point in the quality chain.
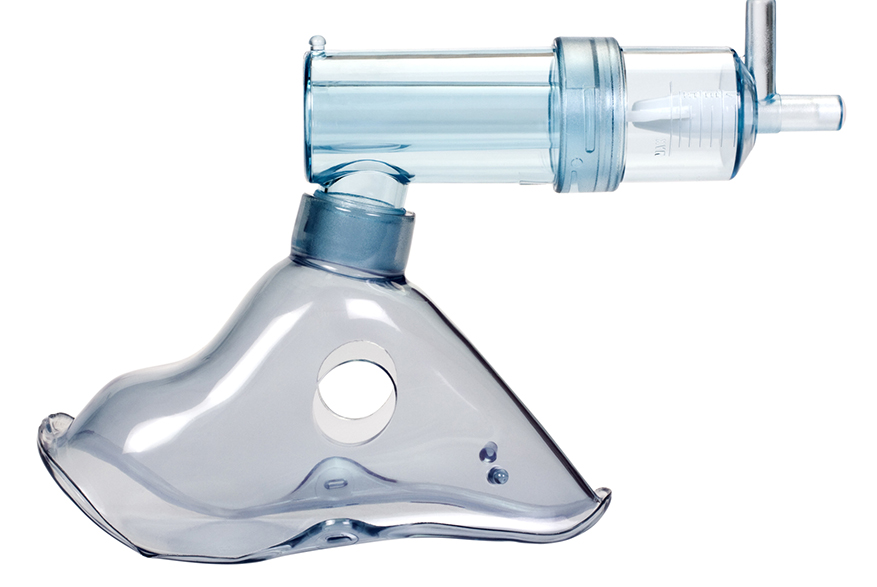
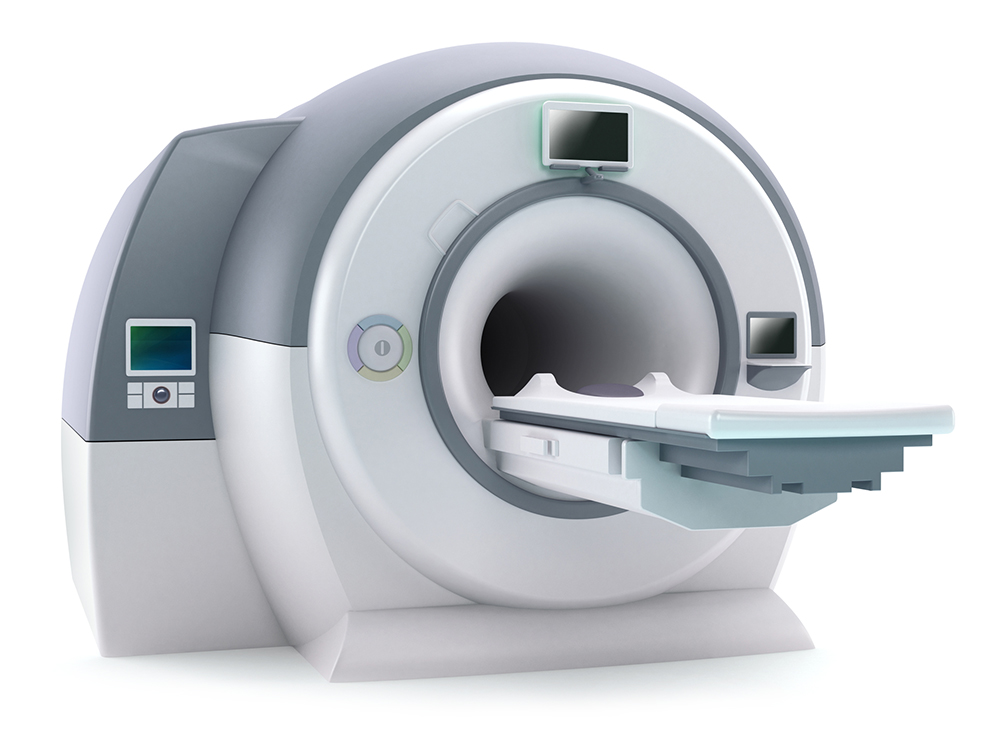
Quality Aligned with Compliance
AssurX makes it easier for your teams to participate in compliance efforts by incorporating regulatory requirements in your system. Configure the system to your organization’s unique compliance demands.
Controls for HIPAA
Electronic PHI is accessible only to those who are allowed to see it. AssurX QMS software gives you the capability to set strict permission rights and shield unauthorized users from records that hold PHI.


Greater Control of Nonconformance Process
AssurX provides a dynamic process for identifying, evaluating, documenting and disposition of non-conforming product as required per FDA 21 CFR 820 and ISO13485. Common terminology, failure codes, and escalation rules enable medical device and diagnostics manufacturers to identify and investigate the root cause of the issue diligently, demonstrate control of the non-conforming product, and use non-conformance data to help improve product quality at the design stage.
AssurX: Connected Quality and Validated Compliance
AssurX provides expert technical and program management oversight for customer deployments around the globe. We employ a structured implementation process, providing a consistent method for architecture design.
AssurX: Quality & Compliance Systems for Every Enterprise
AssurX has been serving the medical device and diagnostics industry for more than two decades. Companies worldwide turn to us for help in reducing regulatory burden by automating quality processes while also demonstrating compliance.
We can help you establish a new medical device quality management system or improve your existing system. Using unconnected ERP, PLM, and other enterprise applications? We can integrate them for a holistic approach to compliance and optimal usage.
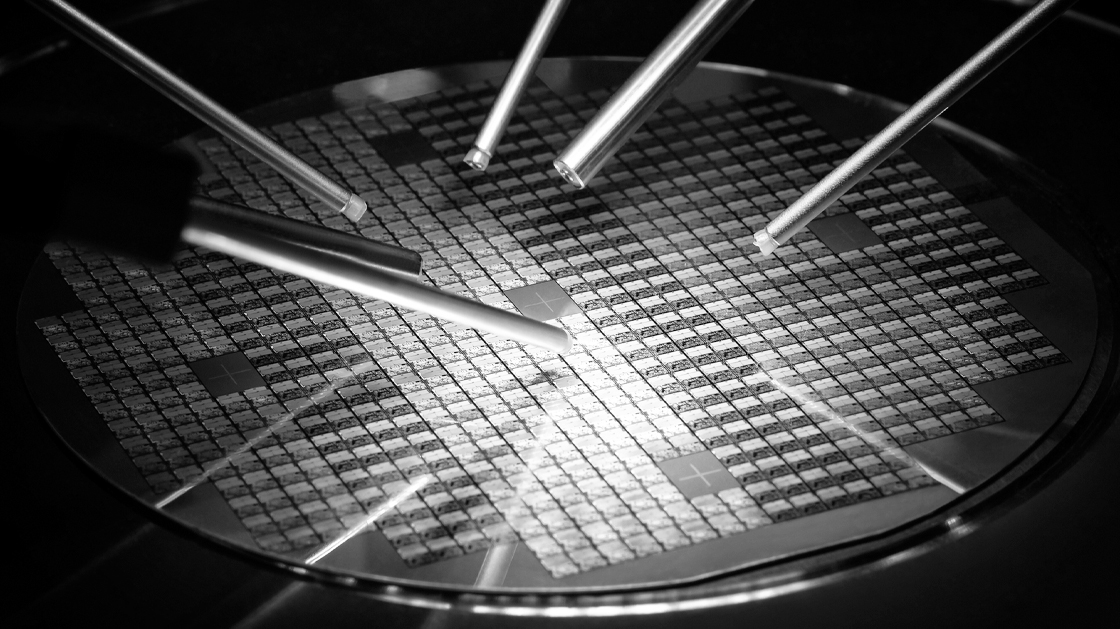
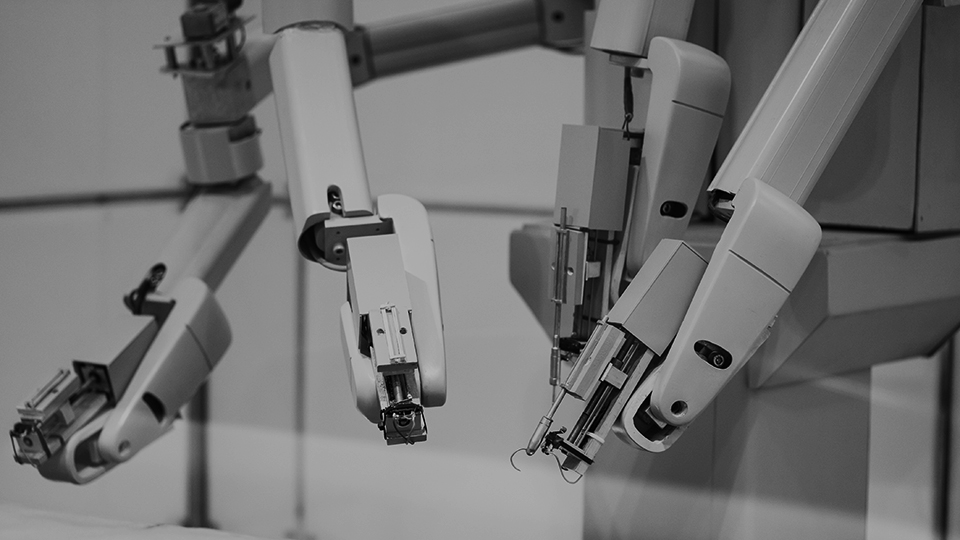

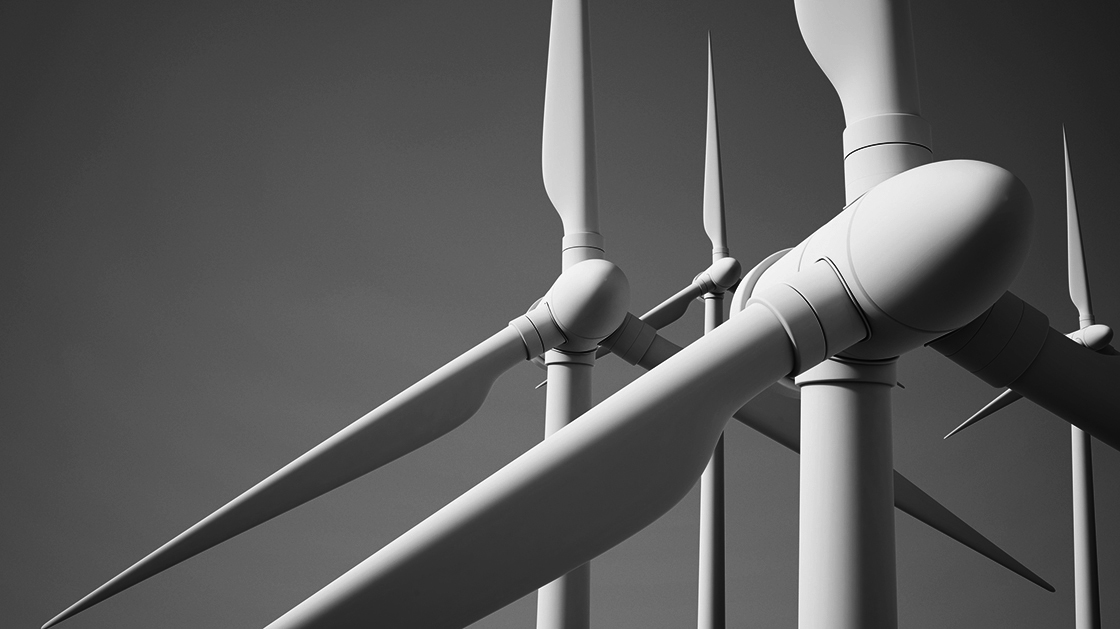
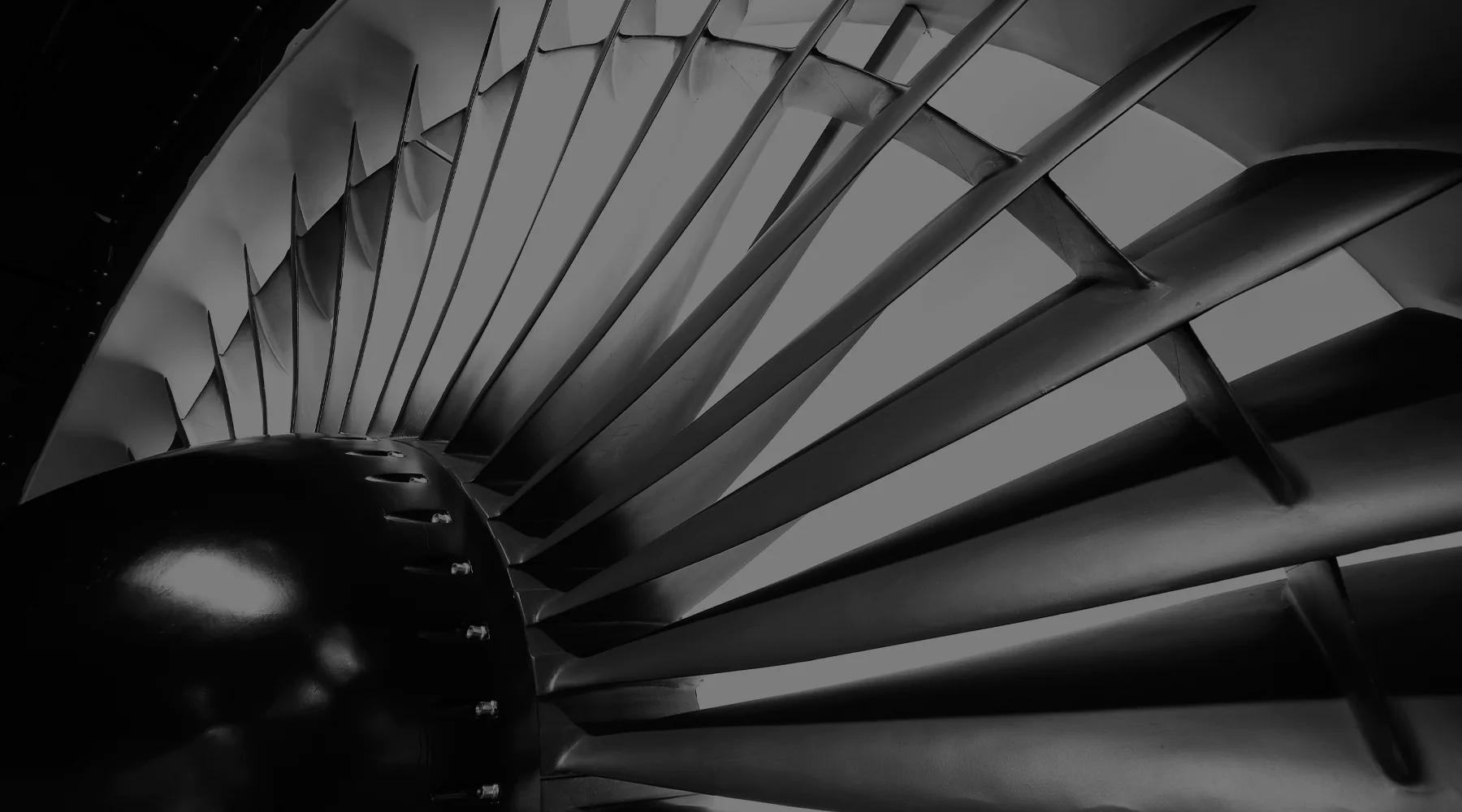

One Platform. Every Solution.
Seamlessly integrate all quality and compliance processes with one software system. Start by using just the solutions you need now, then easily add more as you are ready. No other system is easier to deploy, configure, and modify.