Reduce Manufacturing Costs and Quality Failures
Build Trust and Confidence in Measurement Reliability
Calibration Management Software
AssurX Calibration Management Software helps regulated medical device, pharmaceutical, and high-tech manufacturers quantify, control, and demonstrate acceptable device measurements. It captures all the required data used for calibration measurements (safety, quality, and environmental). In addition, the module is designed to simplify data storage by retaining all information in one centralized location.
The AssurX calibration quality management solution relates to the ISO 9001 Standard for Quality Management Systems. The standard defines calibration as a documented comparison of the measurement device to be calibrated against a traceable reference standard/device (the “calibrator”). Validation of calibrations aligns with NIST standards for the US.
AssurX enables you to identify assets that require calibration and the characteristics, capabilities, functions and features for assets that require calibration. These include serial number, type and maker of the equipment, appropriate tolerance data, initial setup date, and current status.
Establish a consistent approach to calibration management, from tracking and investigation through remediation, corrective actions and preventive actions, and any resulting changes.
Automate Calibration Management for Quality Assurance
AssurX provides powerful process automation to attain compliance and elevate quality standards. Robust configurability with no custom coding allows your organizations to design a calibration process suited to your requirements. A systematic and repeatable process provides assurance that all calibrations are planned, managed and executed in a timely and consistent manner.
Calibration Management Features include:
Benefits of a Standard-Based Calibration Quality Management Software
Trace calibration identification, validation and safeguarding through an auditable, unbroken measurement hierarchy. Request and capture signatures required for the proper closure of calibration tasks. Capture all details of instrument adjustments efficiently and conduct proper closure of calibration tasks.
View all major calibration records and actions in configurable dashboards with drill-down capabilities. Ensure that all measuring devices are properly and timely calibrated for their intended use. Gain insights through reports and analytics to make informed decisions.
Proper calibration protocols are programmed into the application to serve as a QA assurance mechanism for improving the quality monitoring process. Integrate with additional AssurX quality management processes including CAPA, deviation management, document management, training management and change management for a turnkey system.
AssurX Calibration Management Software lets you proactively establish a pre-defined calibration schedule for each asset and track all activities in a centralized system. This creates efficiencies that minimize manual labor hours and eliminate scheduling backups. Your team has more time to focus on improving quality instead of searching for data and being backlogged.
Upload all device/equipment information on any type of calibration. AssurX provides data migration services to help you pull in data from outside sources. In addition, AssurX integration services can create direct connection with MES, CRM, SCADA, or other systems to create a centralized set of specifications.
Define roles to assign person(s) to be responsible for specific equipment. Those people are directly responsible for entering calibration results of that equipment into AssurX. Allow proxy roles for times when the responsible person will be unavailable to maintain a chain of communication and accountability.
AssurX: Quality & Compliance Systems for Every Enterprise
When you choose AssurX, you’re choosing more than two decades of expertise in regulated environments and continuous innovation in quality management. Our unwavering focus on quality management means you’re getting a best-of-class solution, not a scaled down or inflexible software solution.
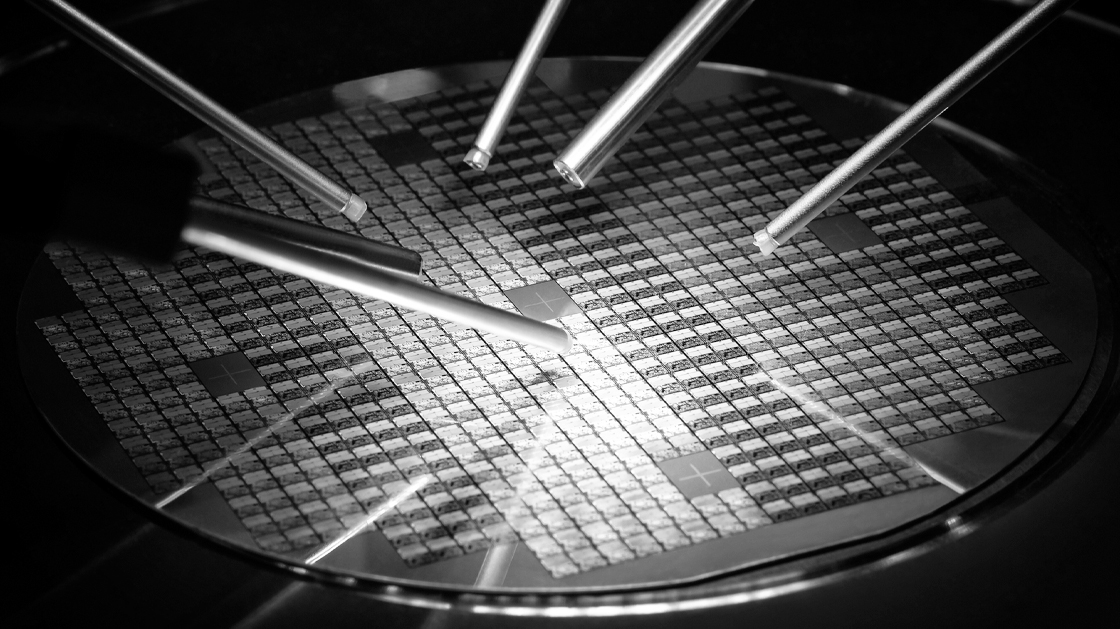
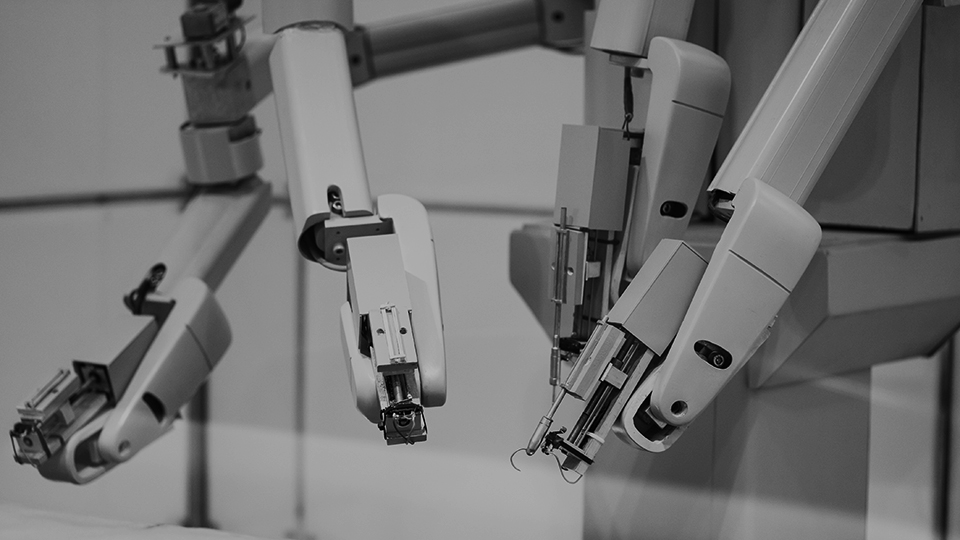

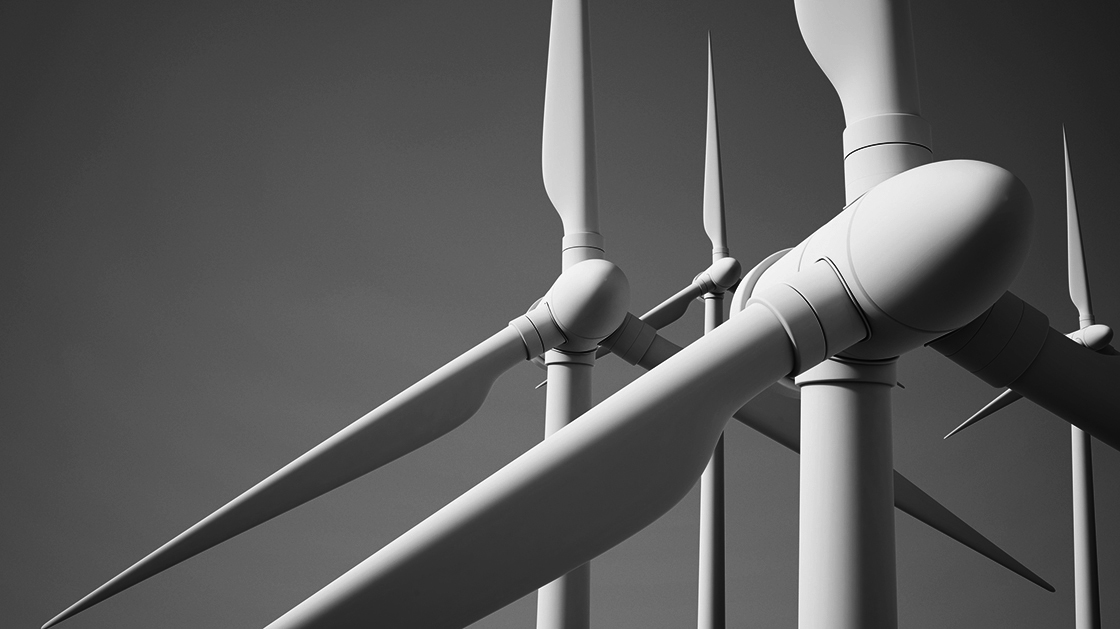
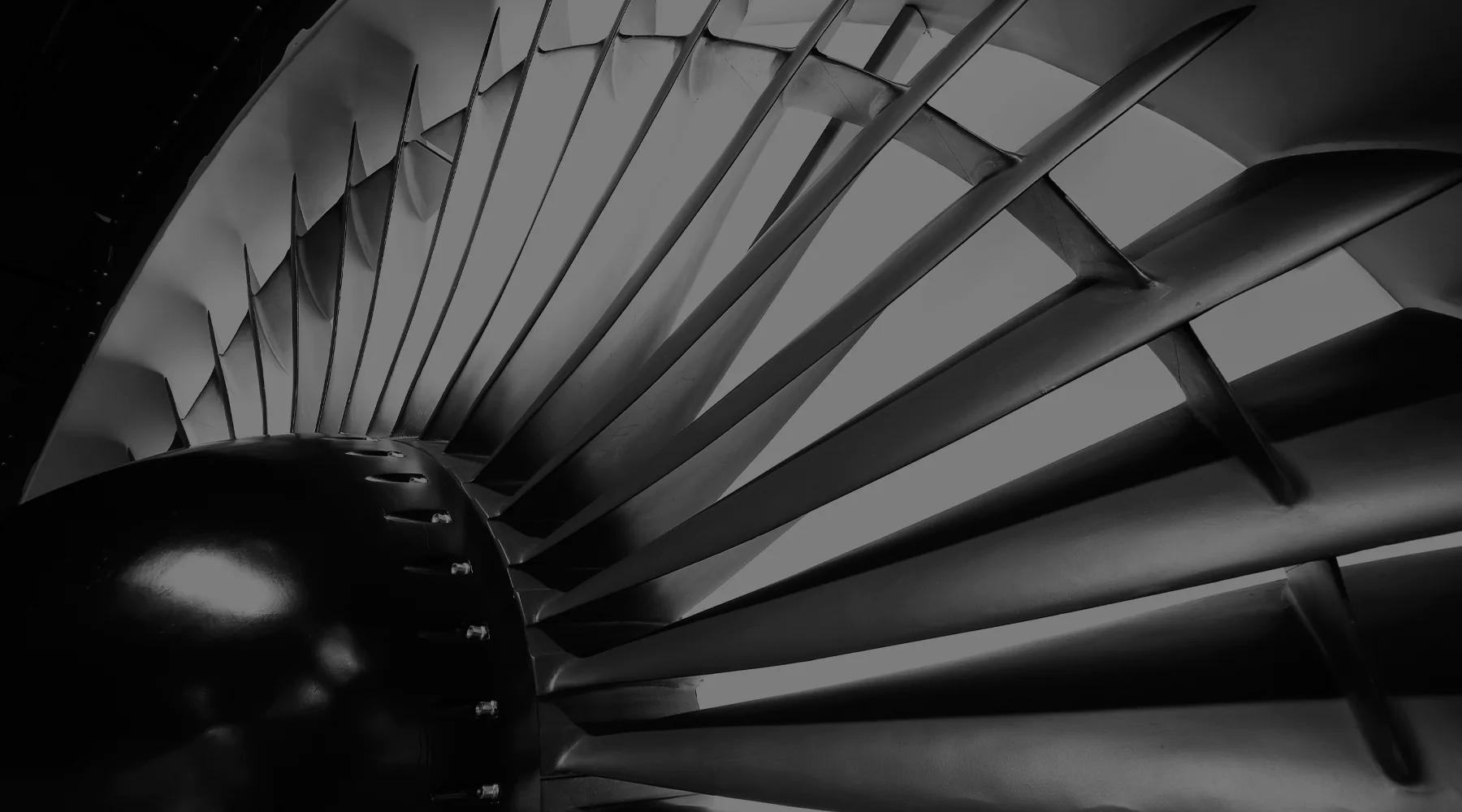

One Platform. Every Solution.
Seamlessly integrate all quality and compliance processes with one software system. Start by using just the solutions you need now, then easily add more as you are ready. No other system is easier to deploy, configure, and modify.